EARTH RODS - LECTRO-TECH - SERVICE LIFE OF EARTH RODS OF DIFFERENT MATERIALS
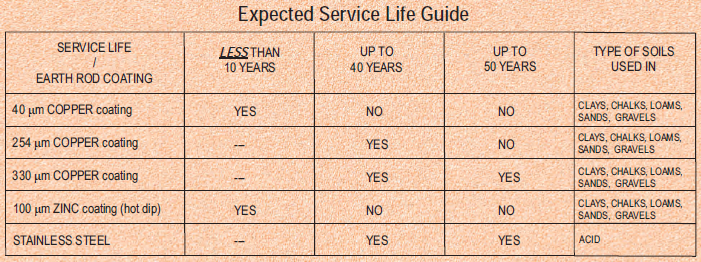
The most commonly used earthing/grounding materials world wide are copper clad steel, copper and galvanized steel. The
effect of earthing/grounding material corrosion on the reliability of electrical installations and electronic equipment is of
paramount importance.
Copper has an outstanding history of corrosion resistance in most underground environments. Copper does not naturally
corrode in most clays, chalks, loams, sands, and gravels. Certain aggressive soil conditions, however, can cause it to corrode.
The basic prerequisite for corrosion is the presence of appreciable amounts of moisture. Other factors that can facilitate the
corrosion process include soils having: elevated concentrations of sulfate, chloride, ammonia compounds, or sulfide; poor
aeration, which supports anaerobic bacteria activity; large amounts of organic or inorganic acid; and large oxygen or neutralsalt
(especially chloride) differentials. Copper is also subject to corrosion by stray DC electricity.
Three studies undertaken in the USA provide a very good guide line for the service life of an earth rod:
1-National Bureau of Standards USA
From 1910 to 1955, the National Bureau of Standards
conducted an extensive underground corrosion study in
which 36,500 specimens, representing 333 varieties of
ferrous, nonferrous, and protective coating materials were
exposed in 128 test locations throughout the United States. It
is widely regarded as one of the most comprehensive
corrosion studies ever conducted.
The time required to remove 254μm of copper can be used
to establish a ground rod’s nominal service life. Although
different soils were used, the data from 8 to 13 years shows
that the rate of corrosion seems to lessen with time. This is
probably due to the protective copper oxide film that
develops on the rod. It can be conservatively assumed that in
the vast majority of soils tested, a service life of far in excess
of 40 years can be expected.
“An analysis of tests of hot dipped zinc showed that in most
of the soils, zinc coatings of 89μm or less were destroyed
during the 10 year exposure period, and pitting of the
underlying steel occurred.”
Additionally, an analysis of galvanized pipe shows an
average penetration of roughly 64μm after 10 years. After 13
years; the average penetration of copper was 0.011938μm.
This study definitively shows the difference in corrosion
resistance between copper and zinc. Copper provides
protection that is several orders of magnitude greater than
zinc.
2-Naval Civil Engineering Laboratory
One of the most useful ‘real time tests’ was conducted in
1960 by the Naval Civil Engineering Laboratory (NCEL) in
the USA on a 7-year program of testing metal rods for
electrical earthing/grounding. Copper-bonded, stainless clad,
and galvanized steel rods were included among other
materials. Samples were buried individually and connected in
pairs to determine the galvanic corrosion effect each rod had
on other metals. Although this study is not nearly as rigorous
as some others undertaken, it does provide an independent
source of information specifically relating to earth rods. |
The study set out to establish the best type of electrode as
determined by the following:
1. It should be easy to drive
2. It should be resistant to corrosion
3. It should not cause galvanic corrosion to nearby
metal.Regarding single rods, these observations were made
after samples were removed following 7 years of exposure:
Galvanized steel rod: “Most of the galvanizing had been
lost. Rusting of the steel was greatest near the surface of the
ground. Pitting was worst here and near the tip.”
Stainless-clad steel rod: “The cladding was free of
corrosion, but at the tip the steel core had corroded to a point
about 25mm inside the cladding.”
Copper-clad steel rod: “The copper cladding was virtually
free of corrosion, but the steel core had corroded at the tip to
a point 50mm inside the cladding.”
The study concluded, “Magnesium, aluminum, zinc, mild
steel, and galvanized steel rods did not have the desired
corrosion resistance.” There was a concern about the copper
clad rod causing galvanic-corrosion to coupled mild steel.
The amount of galvanic corrosion caused by coupling copper
and steel will vary depending on their ratio. Since the ratio of
steel to copper in most grounding systems is usually large,
the amount of steel corrosion is negligible. Additionally, there
are often other sources of copper in the ground, which can
add to galvanic corrosion concerns.
3-National Electrical Grounding Research Project – Pawnee Site Exhumation
The NEGRP was started in 1992 to compare the long-term
performance of different types of earth/grounding electrodes.
In 2003, one of the original sites (Pawnee) was excavated
and the rod electrodes removed. 5/8" (16mm dia) copper-
bonded and 3/4" (19mm dia) galvanized rod samples were
exhumed. The results were definitive. The 5/8" (16mm dia)
copper-bonded rod was virtually free of corrosion while the
3/4" (19mm dia) galvanized rod showed significant
deterioration. |
|
REFERENCES
1. “Underground Corrosion,” Melvin Romanoff, United States Department of Commerce, National Bureau of Standards, Circular 579 (April 1957)
2. “Field Testing of Electrical Grounding Rods,” Naval Civil Engineering Laboratory, Naval Facilities Engineering Command, Technical Report R660 (February 1970)
|